Surface and Finishing Quality Exploration of Complex Cast Glass Forms Produced on Disposable Moulds
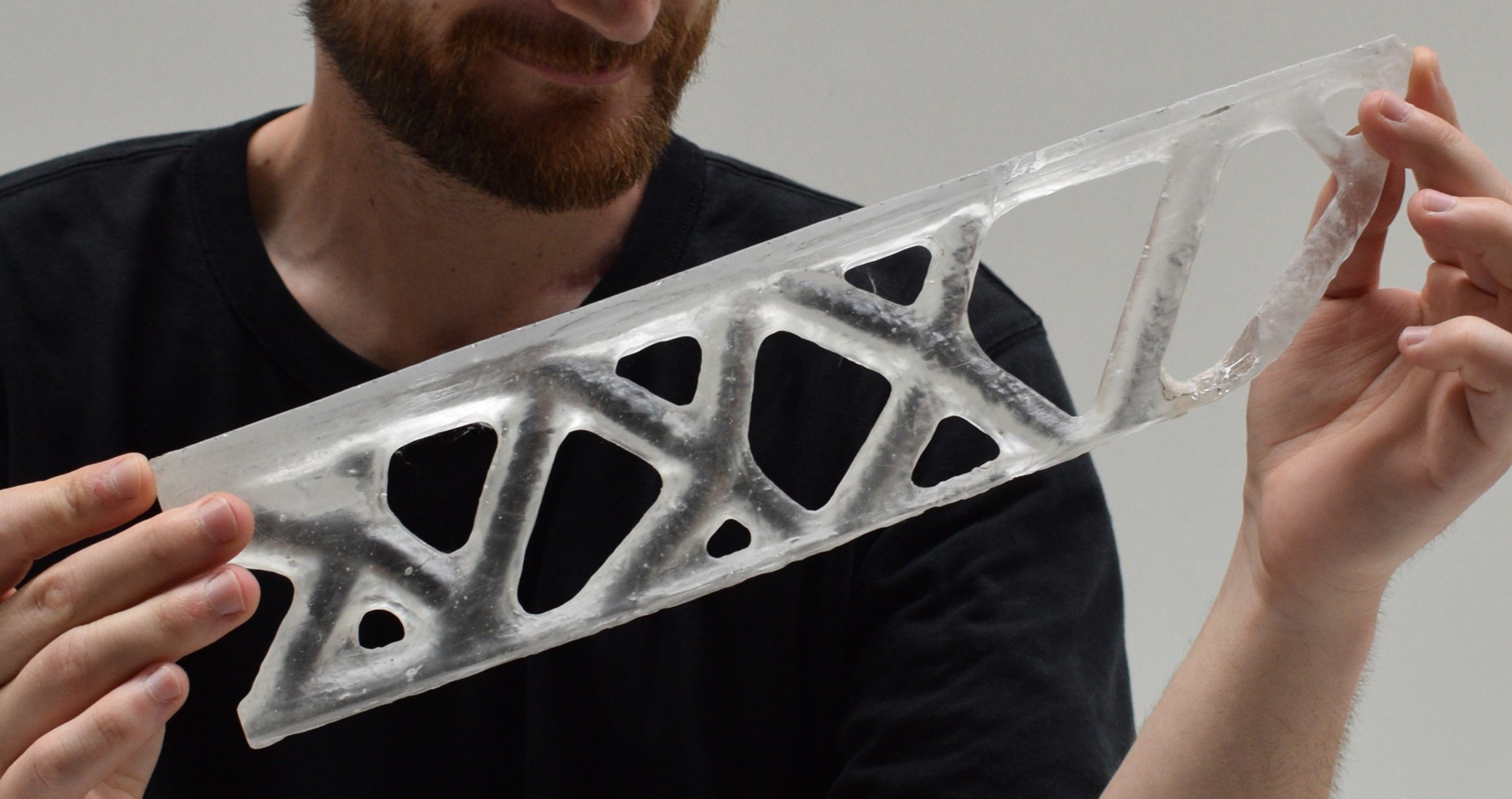
Abstract
Glass casting displays great forming potential allowing for the realisation of three-dimensional glass elements of virtually any shape and size, as showcased in glass art. Disposable mould technology seems to be ideal for the fabrication of such customised and complex geometries, including for architectural and structural cast glass components deriving from structural Topology Optimization (TO), since it offers great shape freedom and cost effectiveness. However, currently, glass casting on disposable moulds faces the major drawback of a resulting rough and opaque glass surface quality, requiring considerable post-processing to yield a glossy, smooth surface. This in turn results in a compromised dimensional accuracy and on increased time and production costs. If the surface remains unprocessed, it can greatly affect not only the visual but also the mechanical properties of the cast glass element. Aim of this research is to improve the surface quality of complex glass components cast in disposable moulds, directly during demoulding, reducing in this way the need for post-processing. To achieve this the research focuses on exploring ways to pre-process disposable moulds. In specific, the research focuses on series of kiln-cast laboratory experiments at various maximum firing temperatures / annealing schedules involving the use of two different types of disposable moulds, 3D-printed sand moulds (3DPSM) and silica plaster moulds (Crystalcast®), and the application of refractory coatings, coating combinations and protective layers. The experimental work conducted thus far indicates that the best results are obtained at the lowest maximum temperature tested (870oC), with the combination offering the best finishing quality to be a synthetic (ceramic) sand mould coated with Crystalcast® and Zirkofluid® (6672, 1219). Scaling-up of the kiln-cast prototypes unveils a complex correlation between the maximum dwell time at the maximum firing temperature and the casting effectivity/ performance of mould materials and coatings.
Published
Issue
Section
Cast Glass
License
Copyright (c) 2024 Menandros Ioannidis, Faidra Oikonomopoulou, Telesilla Bristogianni, Marcel Bilow, Anna Maria Koniari

This work is licensed under a Creative Commons Attribution 4.0 International License.