Investigations on the Cold Bending Behaviour of a Double Glazing Unit with a Rigid Edge-Spacer Frame
DOI:
https://doi.org/10.47982/cgc.8.422Downloads
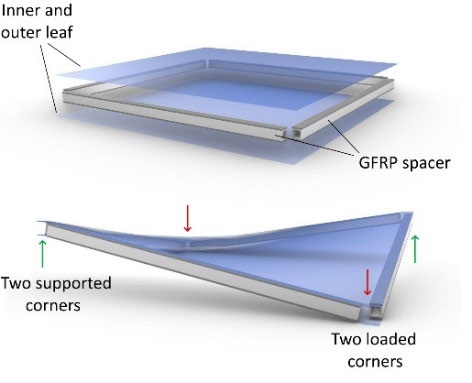
Abstract
Free-form façades with bent glass are becoming increasingly popular. As bending glass provides it with a better resistance to out-of-plane loads, it can result in thinner glass. A promising new technique is to cold bend thin glass plates with a stiff structural edge into a hyperbolic paraboloid (hypar), and to subsequently lock the corners to create a self-contained, self-stressed system. In this study, the bending process of specially-fabricated double glazing units (‘panels’) is investigated with a focus on a local instability phenomenon. The hypothesis that this instability is affected by edge stiffness of the plate, is tested by using 30x30 mm GFRP profiles as spacers along the perimeter of the glass. These were bonded to the glass using Dow 993 silicone adhesive. Four 1.5x1.5 m panels were produced in total, three with 4mm fully toughened (FT) glass, and one with 1.1 mm chemically toughened (CT) glass. The panels were cold bent in a series of laboratory experiments. A numerical model was developed to provide further insight on the mechanical response and to predict the outcome of the experiments. With the sizes of panels used it was not possible to form a hypar. Due to the small thickness of the glass, one the diagonals would always straighten when cold-bent. The 4 mm FT panels failed when the bottom plate fractured at a corner displacement of around 150 mm and a total load of 2.6 kN. The bottom plate of the CT 1.1 mm was also the first to fracture, at a corner displacement of 120 mm and a total load of 1.4 kN. The top and bottom plates came into contact in the centre of the plate when the corner displacement was around 50 mm for the FT 4 mm panels, and around 30 mm for the CT 1.1 mm panel. The numerical model predicted this contact and the overall behaviour of the panel up to a corner displacement of 60 mm. It was concluded that the glass was too thin to create a hypar with this panel size. The experimental data generated along with the numerical model are useful for future research and developments.
Published
Issue
Section
Insulating Glass Units
License
Copyright (c) 2022 Tim van Driel, Chris Noteboom, Mauro Overend

This work is licensed under a Creative Commons Attribution 4.0 International License.